Momentary Pushbutton Switch Circuit with Sensing Loop
Initially, I didn't want a switch on the front of the power amps. However, given the soft start circuits, it seemed best to provide them. Indeed, the soft start circuit does support remote triggering, e.g. by a pre-amp, but let's not go there.
So, if I was to provide switches I wanted them to be nice like the Bulgin vandal-resistant series.
Buglin Anti-vandal Switch
As it happens AMB provides a PCB to support momentary pushbutton switchs. This is the Epsilion 24 (e24). This neat little board also provides dual LED support for the switch (to provide an indication of fault conditions) and supports thermal sensor arrays.
The e24 requires its own dedicated power supply. This can be provided by a miniature transformer and a PCB, the Sigma 24 (s24), is also provided by AMB.
I won't go into the workings of the e24, but essentially it allows the switch to be used to activate an off board relay. This relay breaks the live connection to the soft start circuit. The e24 also has an additional onboard relay which is triggered by devices on the sensor loop. When the sensors are triggered, they cause the onboard relay to act as though the switch had been pushed and switch off the power to the amp.
The sensors I have chosen are thermal devices. They are very much like switches and can be fixed onto heat sensitive components. They are ordinarily open (off). When a threshold temperaure is reached they close (on) and trigger the relay to turn off the amp. The plan is to attached the sensors onto the chips. I have selected variants which close at a temperature which is within the safe upper bound temperature of the chip.
Thermal Switch
I have built the e24 and s24, so here are a few pictures.....
e24 PCBs
I've got three of these boards; one for each power amp and one for the pre-amp. Not sure which pre-amp I'll build yet. Something with valves might be nice.
e24 PCBs populated with components.
The e24s were easy to build and no issues were encountered along the way. That said, I haven't actually tested them yet.
s24 PCBS.
Here are the corresponding three s24 PCBs....one per e24.
e24 and s24 PCBs populated with components.
Again, no issues with construction to report.
The transformer provides 12VAC. The rectifier to convert AC to DC is held on the e24. After rectification, about 17VDC is provided. A regulator is used to drop this down to the required 12 VDC. A stable voltage, as provided by the regulator, is required to prevent false triggering of the circuitry because fluctuations in voltage can fool the circuit into thinking the pushbutton switch has been pressed.
Power switch components for one amp.
So, in the centre is the e24 with the s24 directly behind it. To the left of the e24 is the relay which switchs the main power supply to the soft start circuit. To the right are the thermal sensors. At the front is the push button switch.
The e24 is designed to sit on top of the s24, making for a much more compact component.
Initially, I didn't want a switch on the front of the power amps. However, given the soft start circuits, it seemed best to provide them. Indeed, the soft start circuit does support remote triggering, e.g. by a pre-amp, but let's not go there.
So, if I was to provide switches I wanted them to be nice like the Bulgin vandal-resistant series.

Buglin Anti-vandal Switch
As it happens AMB provides a PCB to support momentary pushbutton switchs. This is the Epsilion 24 (e24). This neat little board also provides dual LED support for the switch (to provide an indication of fault conditions) and supports thermal sensor arrays.
The e24 requires its own dedicated power supply. This can be provided by a miniature transformer and a PCB, the Sigma 24 (s24), is also provided by AMB.
I won't go into the workings of the e24, but essentially it allows the switch to be used to activate an off board relay. This relay breaks the live connection to the soft start circuit. The e24 also has an additional onboard relay which is triggered by devices on the sensor loop. When the sensors are triggered, they cause the onboard relay to act as though the switch had been pushed and switch off the power to the amp.
The sensors I have chosen are thermal devices. They are very much like switches and can be fixed onto heat sensitive components. They are ordinarily open (off). When a threshold temperaure is reached they close (on) and trigger the relay to turn off the amp. The plan is to attached the sensors onto the chips. I have selected variants which close at a temperature which is within the safe upper bound temperature of the chip.

Thermal Switch
I have built the e24 and s24, so here are a few pictures.....
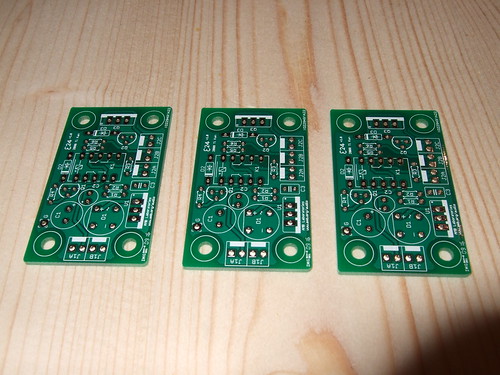
e24 PCBs
I've got three of these boards; one for each power amp and one for the pre-amp. Not sure which pre-amp I'll build yet. Something with valves might be nice.
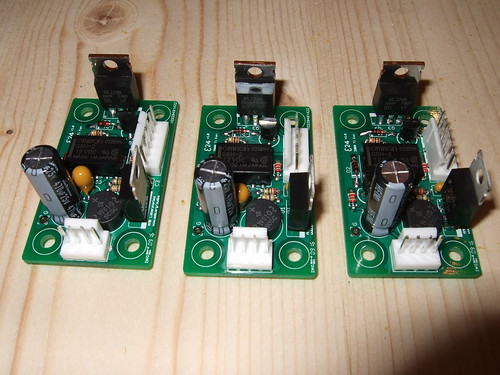
e24 PCBs populated with components.
The e24s were easy to build and no issues were encountered along the way. That said, I haven't actually tested them yet.
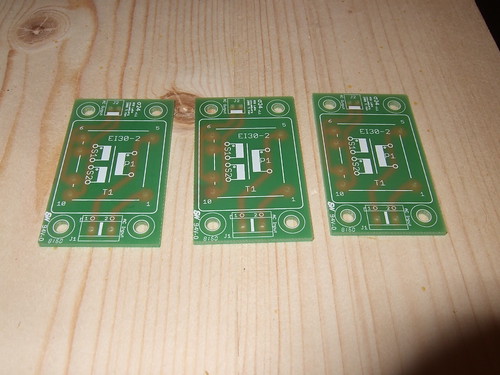
s24 PCBS.
Here are the corresponding three s24 PCBs....one per e24.
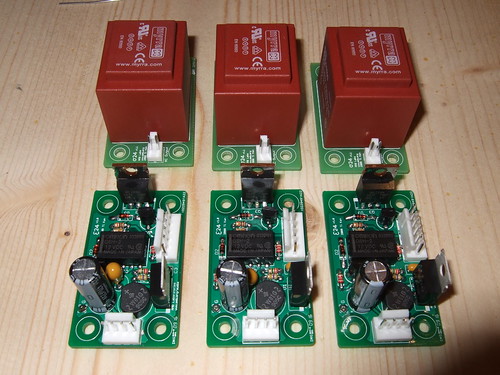
e24 and s24 PCBs populated with components.
Again, no issues with construction to report.
The transformer provides 12VAC. The rectifier to convert AC to DC is held on the e24. After rectification, about 17VDC is provided. A regulator is used to drop this down to the required 12 VDC. A stable voltage, as provided by the regulator, is required to prevent false triggering of the circuitry because fluctuations in voltage can fool the circuit into thinking the pushbutton switch has been pressed.
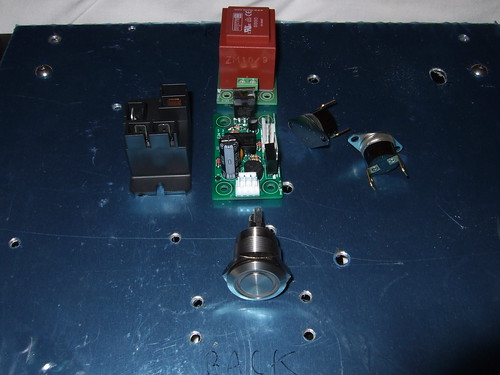
Power switch components for one amp.
So, in the centre is the e24 with the s24 directly behind it. To the left of the e24 is the relay which switchs the main power supply to the soft start circuit. To the right are the thermal sensors. At the front is the push button switch.
The e24 is designed to sit on top of the s24, making for a much more compact component.